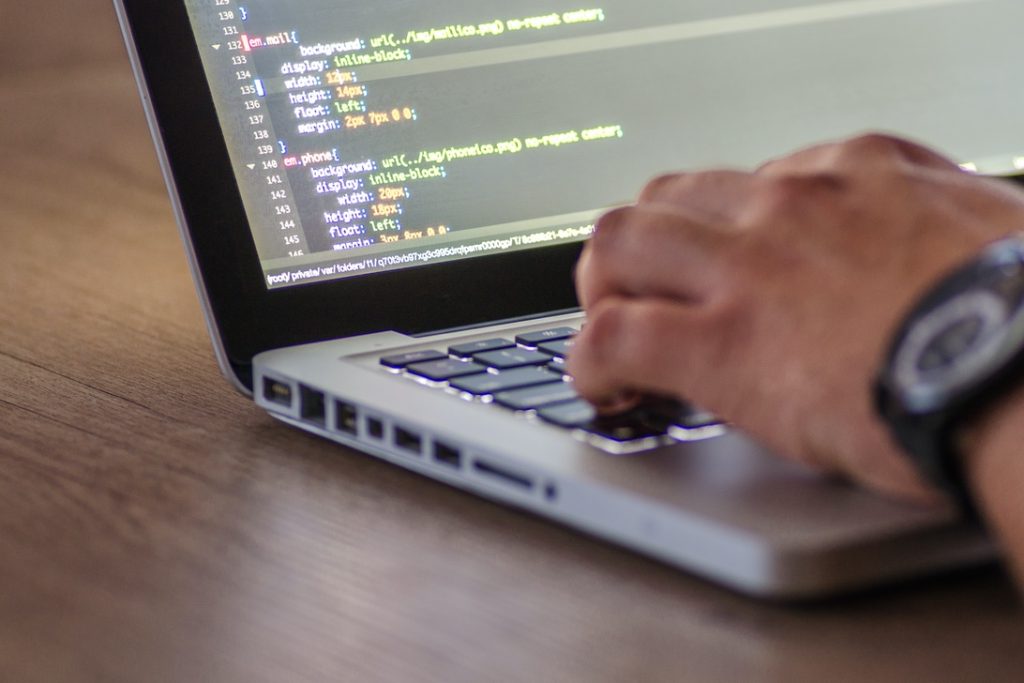
In recent years there has been a growing trend for shipping to be more digitalised. The benefits of more digitalisation are claimed as vessels being more efficient and economic, improved safety, less pollution and GHG emissions, ability to have remote surveys and much more.
There is some merit in these claims although some of the claimed benefits are doubtful to say the least. Many of the new systems and equipment are marketed as being ‘plug and play’ or ‘fit and forget’ with the advantages they bring expected to begin to flow immediately and for all time. What is often overlooked in the initial decision to purchase and later during service, is that most of these systems do need to be kept under constant review as regards the software or firmware version installed and in use.
Seafarers should not be unused to updating essential systems as they have after all been doing just that in the analogue era with charts and nautical publications being required to be current at all times. That said, a good number of ships have been detained over time for not doing that so there is maybe a lack of commitment on some ships. Chart updating has changed in recent years with the advent of electronic charts and ECDIS. Ships can now choose to be electronic and paper or electronic only. They can even still use paper charts as the main navigation method but must maintain ENCs on the mandatory ECDIS.
With two ECDIS systems on board, the requirement to update paper charts has become obsolete on some ships but it must not be forgotten that an ECDIS is only as good as its operating system and sometimes that needs to be updated itself. Maintaining an ECDIS’ software is vital because it ensures the system meets the current standard mandated by the IMO.
When first purchased it is likely that the ECDIS maker will advise all owners when a new software version is released. But as ships change hands and maintenance regimes end, keeping the ECDIS up to date may be overlooked. The result could very easily be a detention by Port State Control because as stated in IMO SN.1/Circ.266 on maintenance of ECDIS software, “ECDIS that is not updated for the latest version of IHO standards may not meet the chart carriage requirements as set out in SOLAS regulation V/19.2.1.4”.
An example of the laxity with which chart updating might be tainted even in the electronic age of ECDIS and Electronic Navigation Charts is that during in a Concentrated Inspection Campaign carried out by the 47 member states of the Paris and Tokyo Port State Control in 2017, some 3.8% of ships inspected reported deficiencies in having up to date electronic navigation charts or ECDIS backups.
Deficiencies in ‘safety of navigation’ which includes this aspect average around 10% of all deficiencies each year in PSC statistics making this the second most common reason for detainable deficiencies.
Electronics appear in many more systems than charting. For example, the AIS, communications systems, engine management, loading computers and much more are commonly controlled by computers even if they do not immediately appear to be. When developing electronic equipment, manufacturers produce an operating system or firmware to control the functionality of the device or system but as with all things, something vital may be overlooked and need to be added and bugs and glitches can occur in uncommon procedures that operators may decide to use. Feedback from users prompts many of the changes. When these become known and also when a new regulatory requirement may be added, the makers release a new version of the firmware. This can happen quite frequently – one model of AIS has had no less than six firmware versions released in three years and that is about par for the course.
Communication management systems that connect together multiple systems and different makers equipment and which determine message priorities and allow the best transmission method for messages may need regular updating to work effectively. Each new version of software will add functionality and may need to be installed each time new equipment is added to the network. Because these systems are normally used with subscription services, the service provider will normally advise when a new version of software becomes available. They will also advise how to obtain and install the new software.
Updating methods will vary according to the machine type and manufacturer. Some may require the equipment to be connected to the internet but most commonly an SD card or USB flash drive is used.
The overall process of firmware upgrading is not that difficult, but it is essential to follow the manufacturer’s instructions exactly. Sometimes a video clip is available to demonstrate the process. The first step is determining what version is running on the equipment and whether an update is needed. This may mean selecting a menu choice or following a set sequence of control button activations.
The next steps involve downloading the new version onto a PC or tablet, unzipping it if necessary, transferring to the appropriate accessory and then connecting that to the device to be upgraded. A reliable power supply for the device during upgrading is essential if the risk of damage (sometimes terminal) is to be avoided. If there is any doubt as to how the update should be done it is best to postpone until an experienced technician can do it.
On some systems and devices, updating is performed regularly whenever connected to the Internet if appropriate settings have been activated. This is how Microsoft updates its Windows Operating System and many other software providers do the same.
It is essential that some checks are carried out before any unscheduled updating process is begun. Many cyber attacks are initiated using a phishing email that purports to come from a manufacturer or supplier and which contains clickable links but is actually sent by a hacker. This could allow a whole IT network on the ship to be compromised.